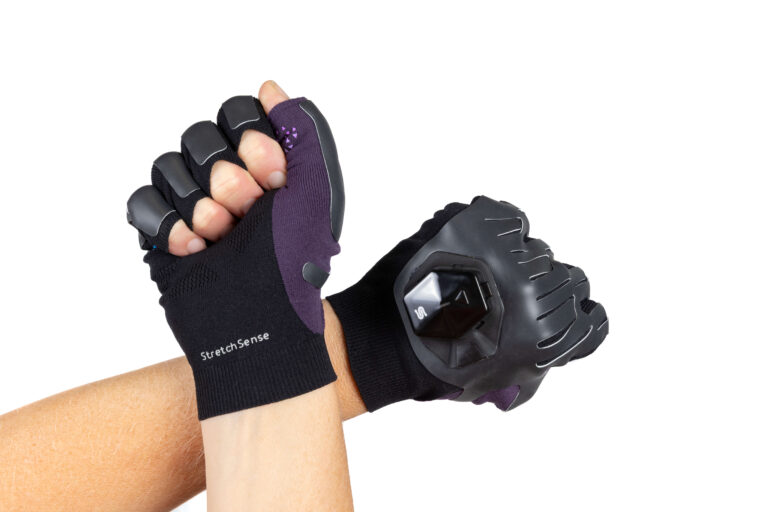
Beyond Sight and Sound: Why Real Immersion in XR Depends on Gloves, Not Cameras
When people talk about “immersive technology,” they usually mean what they can see and hear. And to be fair, we’ve made huge progress there with lighter headsets, sharper displays and advancements in spatial audio. But ask anyone who’s tried to